Aerospace – Operational Improvements
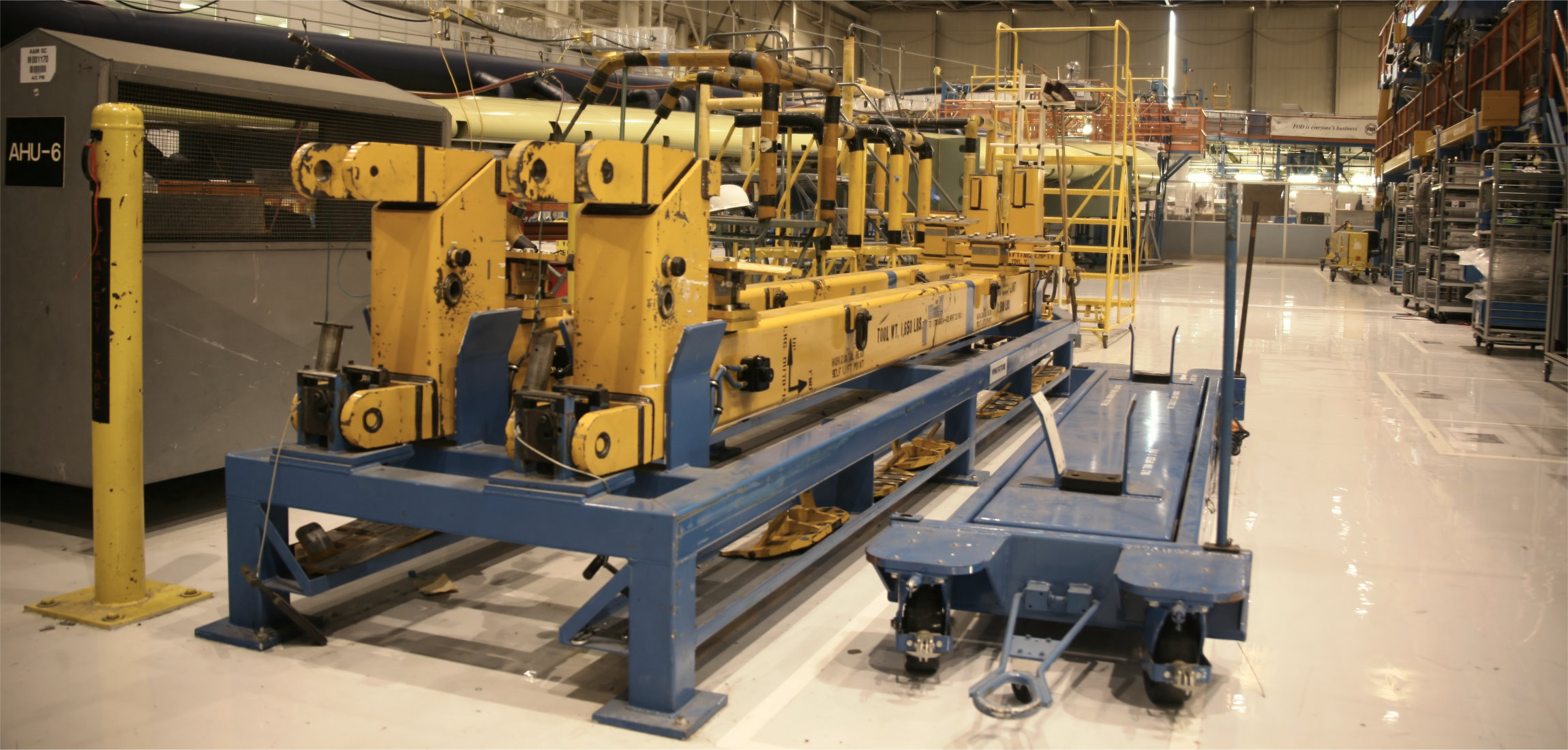
Brief
Rigby Morrison was asked by a global facilities management provider to improve the TFM operation at a 30-acre aerospace manufacturing and production facility covering multiple locations. This, with a view to achieving contract extension, due to ongoing operational issues, and a subsequent lack of client confidence. The team onsite consisted of 4 engineers, a Technical Services Manager, 4 cleaners, a cleaning supervisor, and a 3 person administration.
Solution
The first action taken was to revise the hard services delivery through focusing on efficient scheduling of planned maintenance, and effective deployment of engineers for reactive maintenance. This was a significant change to the standard in which the team were used to operating, and required strategic persuasion in order to gain their trust and confidence that the new operating processes and procedures would be beneficial.
The second focus was on a disorganised and misdirected cleaning operation. Similar to the hard services, the cleaning operation was void of any efficient and effective processes and procedures, however, this challenge was greater due to an appalling sickness culture. Rigby Morrison firstly addressed the sickness issue by implementing and driving the HR sickness policies and procedures of the FM service provider that were previously deliberately overlooked. And finally, to resolve the absence of process Rigby Morrison reviewed and rewrote the cleaning schedules and developed processes and procedures that met the contractual requirements.
Results
The audit produced 38 recommended improvements and uncovered 12 best practice actions, achieving an overall score of 71% in an operational environment where Muda was prominent. Although all wastes were found in abundance, the most prominent was defects waste, thus services cannot be guaranteed to be delivered to the customer at the correct requirement, at the first attempt. To minimise this form of Muda, it was recommended that a pre-use check process is utilised and documented, an employee work quality recognition scheme is implemented, along with a Manager/Supervisor quality checking system. These checks recognise both good and bad service delivery, both of which contribute to improving and maintaining quality, and minimising defect waste.
Feedback
Following onsite Rigby Morrison presence for 6 months, the operation was delivering all contractual requirements and realised significant quantifiable improvements in task completion time, task attendance time, in-house service delivery, and sub-contractor management. This restored the trust and confidence of the client and improved the monthly KPI from 87% to 98%, which resulted in being assigned further project works that generated an additional 20% contract revenue, and the contract was extended for a further 3 years.
Recent Case Studies
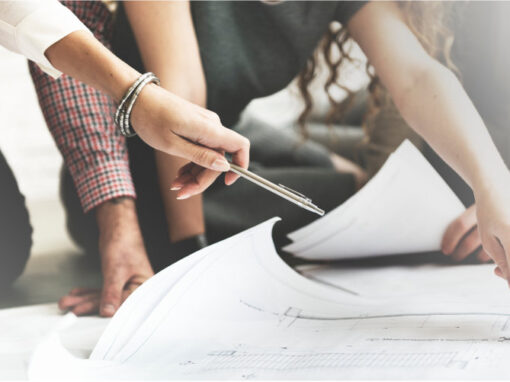
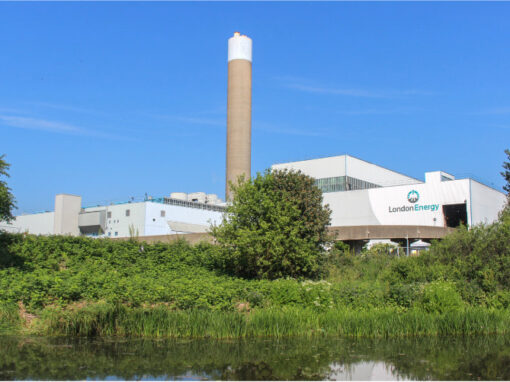
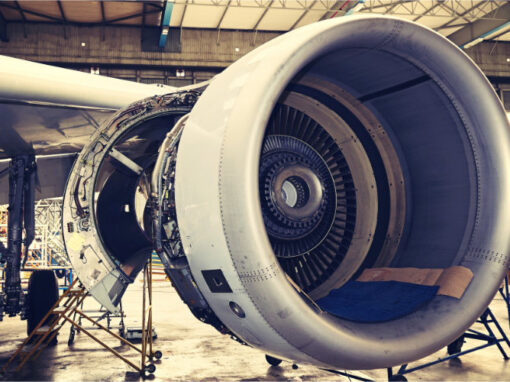
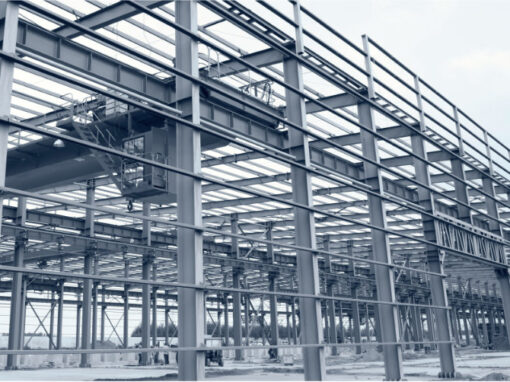
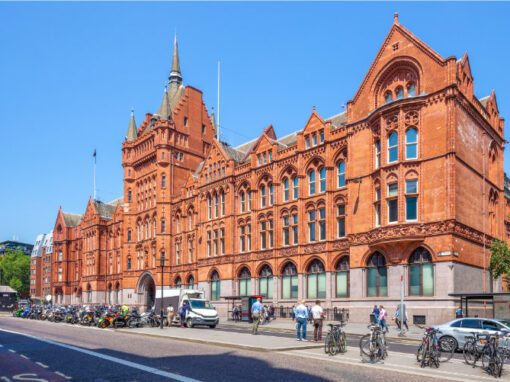
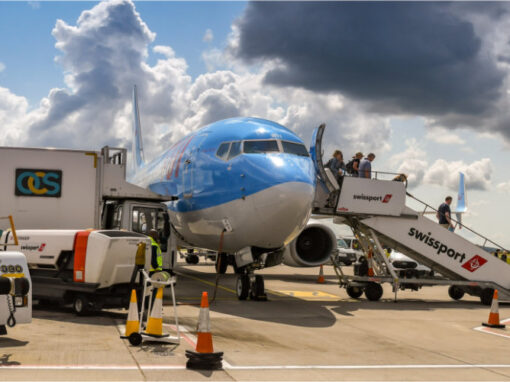
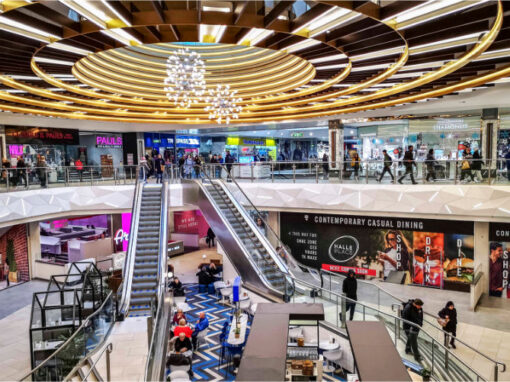
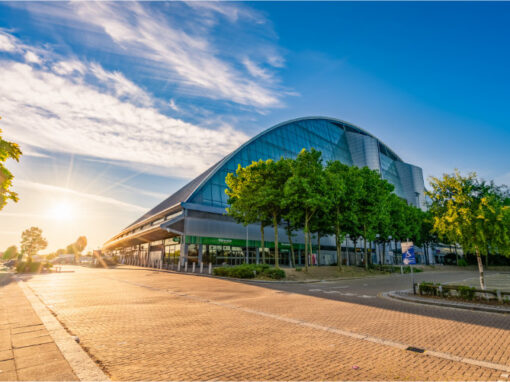
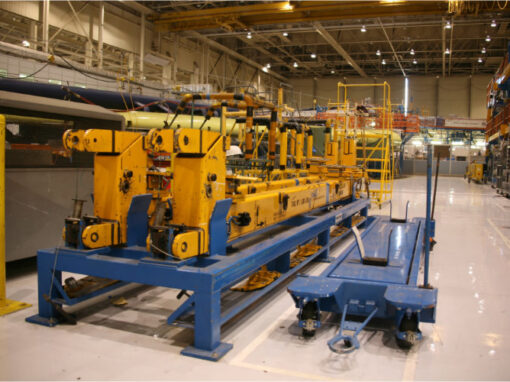
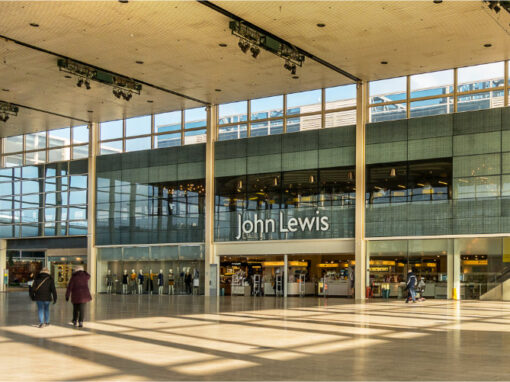
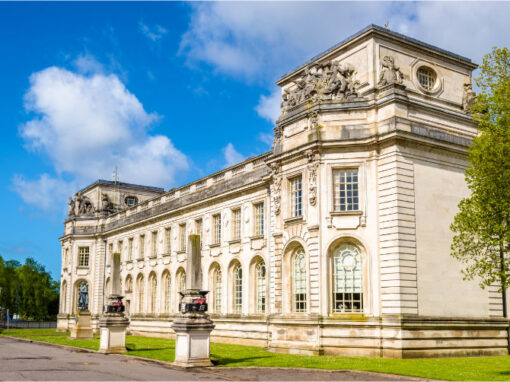
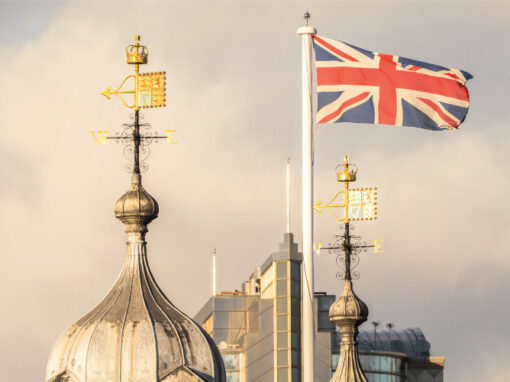
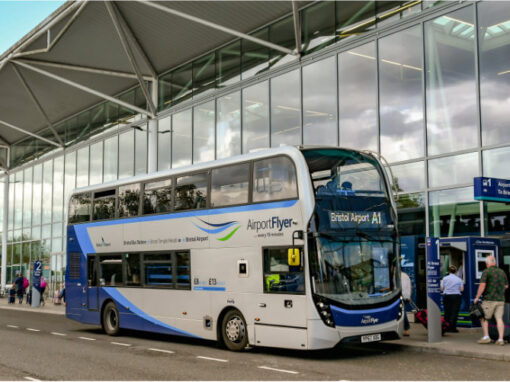
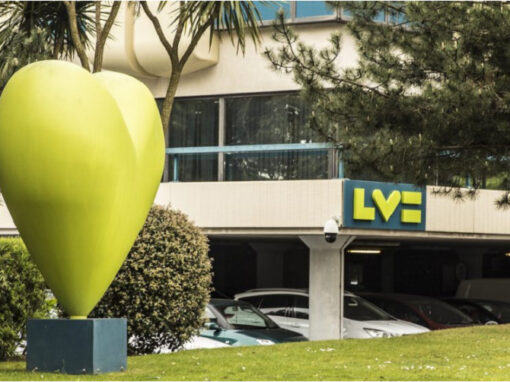
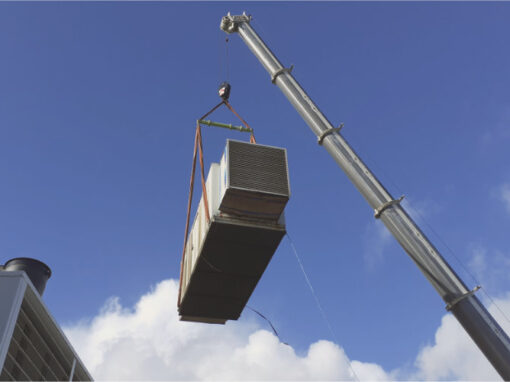